闪耀光栅凭借的定向衍射特性,在光谱仪器中占据核心地位。其加工工艺流程需经过多道精密工序,从基底制备到成品检测,每一步都需严格控制精度,以下是详细流程解析。
1、基底材料制备与预处理
闪耀光栅的基底需选用光学性能稳定的材料,常用熔融石英(透射型)或铝合金(反射型)。首先对原材料进行切割,采用金刚石锯片将石英棒或金属块切割成预设尺寸(如 100mm×100mm×5mm),切割面平面度误差控制在 5μm 以内。切割后的基底进行粗磨,使用 800 目碳化硅砂轮去除表面毛刺和切割痕迹,使表面粗糙度降至 Ra1μm 以下。
预处理阶段的关键是应力消除,将基底放入退火炉中,在 600℃(石英)或 300℃(金属)下保温 4 小时,缓慢冷却至室温,确保内部应力小于 5MPa,避免后续加工中出现变形。随后进行超声清洗,先用 5% 氢氟酸溶液去除石英表面的氧化层,再用超纯水(电阻率≥18.2MΩ・cm)清洗 3 次,最后在百级洁净室中烘干,防止杂质残留。
2、光刻胶涂覆与曝光
在洁净室内,采用旋转涂胶法在基底表面涂覆光刻胶(如 AZ6130)。将基底固定在匀胶机上,滴胶后先以 500r/min 低速旋转 5 秒,使胶液均匀覆盖表面,再以 3000r/min 高速旋转 30 秒,形成厚度为 1-2μm 的光刻胶膜,膜厚偏差需控制在 ±50nm 以内。涂胶后的基底在 80℃烘箱中前烘 30 分钟,去除胶内溶剂,增强胶膜与基底的附着力。
曝光环节采用激光干涉光刻技术,将基底置于精密工作台上,通过 He-Cd 激光器(波长 442nm)产生的两束相干光在光刻胶表面形成干涉条纹。根据闪耀光栅的刻线密度(如 1200 线 /mm)调整光束夹角,确保条纹间距精度达 ±0.05μm。曝光时间需根据胶膜厚度精确控制(通常 10-30 秒),曝光后在显影液(如 AZ300MIF)中浸泡 60 秒,去除曝光区域的光刻胶,形成光刻胶掩模。
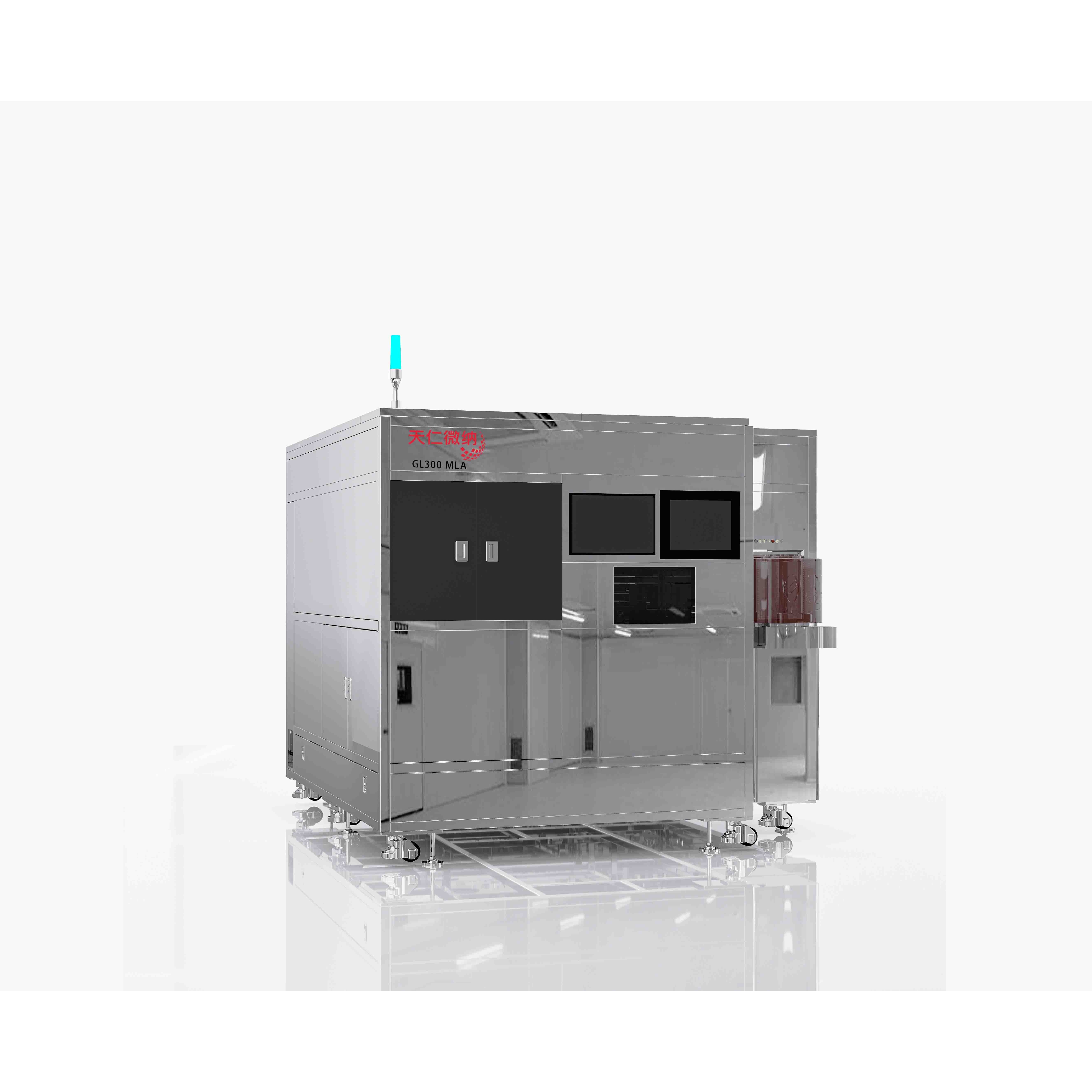
3、刻蚀形成闪耀面
刻蚀是塑造闪耀角的核心工序,透射光栅多采用反应离子刻蚀(RIE),反射光栅则常用离子束刻蚀(IBE)。以金属反射光栅为例,将带有光刻胶掩模的铝基底放入刻蚀腔,通入氩气(压力 0.5Pa),通过射频电源产生等离子体,离子在电场加速下轰击铝表面。
刻蚀过程中,通过调整离子束入射角(与基底法线夹角即闪耀角,如 30°)和刻蚀时间,控制刻蚀深度(通常为波长的 1/4,如可见光波段约 100-200nm)。刻蚀速率需稳定在 10nm/min,通过实时监测光栅表面轮廓,确保闪耀面的角度偏差小于 0.1°。刻蚀完成后,用氧等离子体灰化去除残留光刻胶,露出清晰的光栅沟槽结构。
4、镀膜与后处理
为增强反射型闪耀光栅的光学性能,需在刻蚀后的表面镀制高反射膜。常用铝膜(适用于紫外至近红外)或金膜(适用于红外),采用电子束蒸发镀膜技术,真空度保持在 10⁻⁴Pa 以下,镀膜速率控制在 0.5-1nm/s,膜厚根据波长设计(如铝膜厚度 80nm)。镀膜后进行退火处理,在 150℃下保温 2 小时,提高膜层与基底的结合力,避免使用中脱落。
后处理包括边缘修整和清洁,用激光切割去除基底边缘的多余部分,保证光栅有效区域无毛刺;再次进行超声清洗(频率 80kHz),去除镀膜过程中产生的颗粒杂质,最后用氮气吹干,防止水渍残留。
5、性能检测与质量控制
成品检测需全面评估光栅性能:使用激光衍射仪测量刻线密度,偏差需小于 ±1 线 /mm;通过光谱仪测试衍射效率,在闪耀波长处的效率应≥80%;采用原子力显微镜(AFM)观察表面形貌,确保沟槽深度均匀性(偏差≤5nm)和闪耀面粗糙度 Ra≤1nm。
对于高精度光栅,还需检测波前畸变(≤λ/10,λ=632.8nm)和杂散光水平(≤0.1%)。每批产品随机抽取 10% 进行耐久性测试,在 85℃、85% 湿度环境中放置 1000 小时,性能衰减需小于 5%,确保长期使用稳定性。
闪耀光栅加工流程融合了光刻、刻蚀、镀膜等精密制造技术,每个环节的参数控制直接影响其光学性能。通过严格执行工艺流程和质量检测,才能生产出满足光谱分析、激光技术等领域需求的高性能闪耀光栅。